|
|
 |
|
|
|
|
|
Efficient Quality Assuarance for Tube Manufacturing |
|
|
Optical Tube Measuring System |
|
|
The demand for ever more cost-effective tube production as well as the increasingly stringent requirement for product quality are constant challenges in today's tube bending industry.
Hydrostatic Testing is done through an optical tube measuring system, which incorporates advanced technology for the high-precision measurement of tubes, the determination of set-up and correction data and quality assurance of the end product. Our Hydro Testing process entirely replaces mechanical gauges. |
|
|
|
|
|
How Hydrostatic Testing Works |
|
|
Hydrostatic Testing is done through a contactless measuring system, which merely requires that the tube to be measured is placed in an optical measuring cell. Several high-resolution digital cameras accurately measure the tube's geometry in a few seconds. The tube does not need to be moved. The geometry is reported in an easily understandable way, that is as sheath tolerance. |
|
The measuring range is up to 2,500mm x 1,100mm x 500mm (approx. 8.2 feet x 3.3 feet x 20 inches) and this can be extended by repositioning the tube |
|
Hydrostatic Testing Machine measures tubes with diameters ranging from 4 mm to 20 mm. Bends between 1° and 180° can also be easily measured. TubeInspect has a newly added capability of measuring tubes with connected bends or with flexible parts. With the new FLEX module, it is able to measure tubes with hose-sections, shaped hoses, and hoses with fixtures or mounting attachments. |
|
Our Hydrostatic Testing System enables Tube measurements to be compared with a previously recorded sample part or with an imported CAD model. |
|
 |
|
|
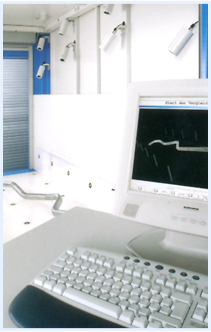 |
|
|
|
|
|
|
|